Polystyrene beads are often mistakenly referred to as STYROFOAM™ beads. The puffing of EPS resin, creating the puffed polystyrene beads is the first step in producing EPS (expanded polystyrene) blocks. Puffed polystyrene beads are used for several different applications besides the manufacture of EPS blocks. Two of the most common are the production of bean bag chairs and the production of lightweight concrete.
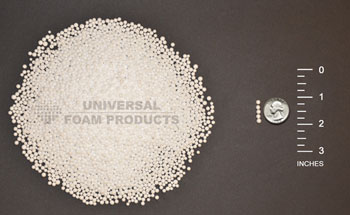

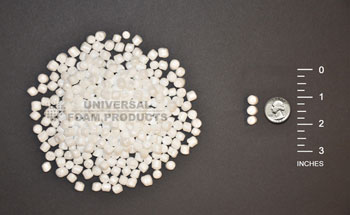
The puffed EPS beads are economical filler with unique properties that can not be obtained using any other material. In construction, the most common use of polystyrene beads is in the production of lightweight concrete. Standard concrete weighs 150 lbs per cubic foot. Puffed polystyrene beads weigh just under 1 lb per cubic foot. There are applications when the strength of concrete is needed but the weight of the concrete is a problem. One solution is to mix puffed polystyrene beads into the concrete mix. As the puffed beads displace the other components of the concrete mix the material becomes lighter. The more beads are added, the less strength the concrete has also, so the final portions are governed by the application of the concrete.
EPS puffed beads are created by applying steam to EPS resin in an enclosed chamber. The Pentane gas in each piece of resin expands from the heat causing the beads to grow by 30 to 35 times their original size. When they are fully puffed the beads are primarily made up of air. The puffed beads are then transferred to a drying chamber where they are subjected to dry air and from there into large poly bags for shipping. For very large applications the puffed beads can be blown directly into a 53’ trailer.
Another major application for puffed EPS beads today is in the manufacture of bean bag chairs and poufs. Bean bag chairs, popular in the 60’s, have seen resurgence in popularity in the past several years. The puffed EPS beads are sold to manufacturers in truckload quantities and blown or poured into the shells using specialized equipment.